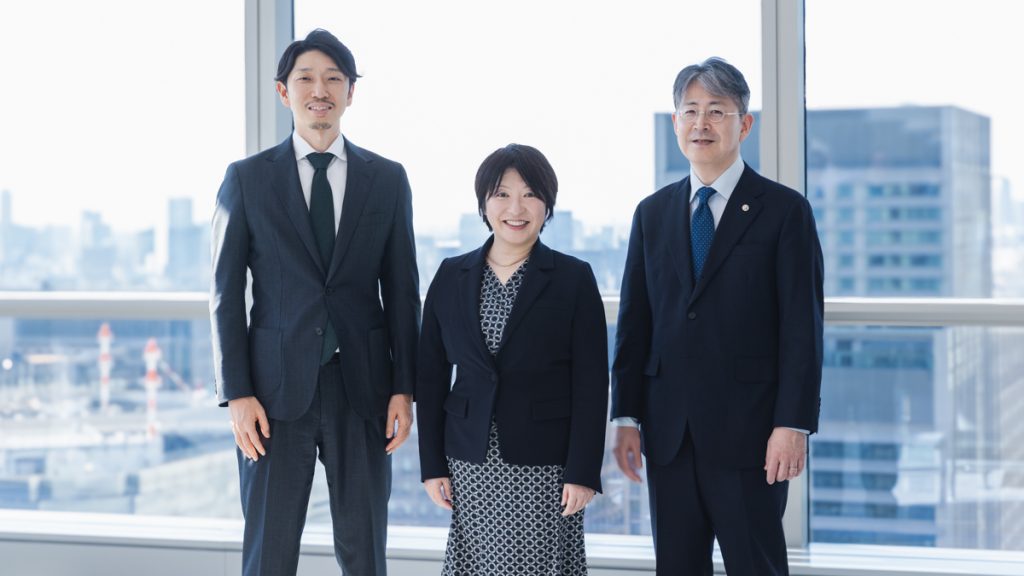
01
2025.04.30(Wed)
Co-Create the Future
2025.03.14(Fri)
#59
この記事の要約
日本触媒とNTTコミュニケーションズは、「AIオートパイロット」を活用して化学プラントの自動運転に成功しました。このプロジェクトは、人手不足や運転品質のばらつき、技能伝承の難しさなどの課題解決を目指しました。特に外部環境の影響を受けやすいデリケートな製品の製造現場が対象です。
NTTコミュニケーションズのチームは、運転員の「何を見て、どう判断し、どう動くか」を徹底的に分析し、AIに学習させました。導入は段階的に行われ、まずはAIがガイダンスモードで推奨値を提示する実験から始めています。
約1年半後、24時間運転のプラントで数日間の連続自動運転を達成。運転員からは「業務負荷が減った」「AIの操作に納得感があった」との評価を得ています。プロジェクト成功の要因は、丁寧なコミュニケーション、段階的な導入による信頼関係構築、そして「一歩踏み出す勇気」でした。
※この要約は生成AIをもとに作成しました。
目次
──日本触媒とNTT Comの取り組みが始まった経緯を教えてください。
伊藤浩二(以下、伊藤):NTT Comは製造業向けのAI技術開発に注力し、2023年に提供を開始したのが、運転員の手動操作を学習したAIによりプラントの自動運転を実現する「AI Autopilot System(以下、オートパイロット)」です。このプロダクトを活用することで、より多くの製造現場の課題解決に貢献したいと考えていたところ、弊社から声をかけさせていただき日本触媒さんとのご縁がつながりました。
野原利夫氏(以下、野原氏):日本触媒ではDX推進本部が旗振り役となり、製造現場のDX化に取り組んでいます。一方、自動化を進めたくてもなかなか進まないという現状があり、NTT Comさんからご提案を受けてこれは良いチャンスではと感じました。社内に持ち帰ると、特に課題の多いプラントから「やってみたい」という前向きな返事があり、オートパイロットを活用した自動運転にチャレンジすることを決めました。
──プラントではどんな課題があったのでしょうか。
佐藤大典氏(以下、佐藤氏):少量多品種でさまざまな化学製品をつくっているのですが、今回対象としたのは、外部環境の影響を受けやすい非常にデリケートな製品の製造現場です。運転員はさまざまな計器情報に目を光らせ、わずかな変化でもすぐにキャッチして適切な操作を行うことが求められます。さらに製造するのは一年のうち数回だけで、その間に担当者が変わることもあり、「運転ノウハウが蓄積しづらい」「教育にかかる負荷が大きい」といった課題がありました。
私は、研究職時代にデータ解析を担当していたことや、製造ではDX推進の一環で統計解析や機械学習を学んだ経験から、「自動化が進めば現場の負荷が減り、新たな価値を生み出せるはず。何か良い手段はないものか」と考えていました。そこに今回のお話が来て願ってもない機会だと、ぜひやらせてほしいと手を挙げました。
──どのようにプロジェクトを進めていったのか教えてください。
藤井沙苗(以下、藤井):まずは会って話を聞かせてくださいとプラントにお伺いしました。初めて現場に入った時に、その迫力とスケールの大きさを目の当たりにして期待と不安が入り交じっていたことを覚えています。私はAIモデルの構築を担当し、まずは過去1~2年分のプロセスデータを解析しました。その後、再び現場に足を運んで運転プロセスに関するヒアリングなどを行い、運転員の操作をAIに学習させるためのモデル構築を進めていきました。
──スタートは順調だったのでしょうか。
藤井:実は苦労の連続でした。そもそも化学の世界に足を踏み入れるのが初めてで、製造工程を理解するのが非常に難しかったのです。はじめはデータを見てもそれが何を示しているのかさっぱり分からず、ただの数字の羅列にしか見えなかったことを覚えています(笑)。
佐藤氏:お互いの認識を合わせるまでには時間がかかりましたが、「これはどういうことですか」「これで合っていますか」と丁寧にやり取りを重ねていったことで、ベクトルが合っていく感覚がありましたね。
伊藤:ある時は「佐藤さんの思考回路を理解させてください!」と、ヒアリングをしながら現場での判断や動きを細かくホワイトボードに書き出したり、佐藤さんが現場で操作している姿をじっと観察したりと、とにかく「現場を知る」ことを重視していました。
佐藤氏:人間が当たり前に行っている操作をAIに学習させるとなると一筋縄ではいかないことがよく分かりました。一緒に現場に入ってもらった時に「今、このデータを確認していましたよね?」と聞かれて初めて、自分が何を見て、どう判断し、どう動いているのかを認識できたことで再発見が多くありましたね。
藤井:運転員の方は目の前に表示されている数値だけでなく、数時間のデータの変動を的確に把握し、それにもとづいて総合的に判断を下していることや、頭の中で複雑な計算を行い、状況に応じて臨機応変に対応しているといったことも会話を重ねる中で徐々に明らかになってきました。本プロジェクトでは弊社が開発した「Node-AI」というAIモデル開発ツールを使っており、現場の皆さんの知見が反映されるようなAIモデルの構築に取り組みました。
──AIモデルを実装するまでにはどのようなプロセスがあるのでしょうか。
藤井:いくつかの段階があり、まずは現場への理解を深めながらAIモデルの構築・検証を行い、オフライン環境で実用レベルまで磨き込みました。そこから実験フェーズに入ります。その際、いきなりAIに運転を任せるのではなく、運転員に対して推奨値を提示するガイダンスモードでの実験を行いました。1分ごとに推奨値が出てくるのですが佐藤さんにその数値に違和感がないかを確認していただき、違和感があればどれくらいの乖離があるのかを明確にし、さらなる磨き込みをかけて実装につなげていきました。
伊藤:悩ましかったのは、製造期間が限られているため、二度目の実験ができるのは数ヶ月後、三度目はまた数ヶ月後と時間が空いてしまうことでした。その間に何もしないのはもどかしいので、AIモデルの動きを確認できるようなシミュレーターを独自につくり始めました。現場を完全再現することは難しいのですが、シミュレーターを使って現場を想像しながらAIモデルの動きを検証し評価を続けていました。
野原氏:数度にわたる実験では思いがけないトラブルが起きたり、プラント設備の仕様変更に合わせてAIモデルを修正いただく必要があったりとさまざまな苦労がありましたね。
藤井:皆さんが快くご協力してくださったおかげで乗り越えることができました。
──プロジェクトの具体的な成果について教えてください。
佐藤氏:取り組み開始から約1年半後、24時間運転のプラントで数日間にわたり連続自動運転を達成することができました。操作は基本的にAIに任せられるため、運転員からは「業務負荷がかなり減った」「AIの操作に納得感があった」などの声があがっています。
運転員にとって「AIをどこまで信用できるか」はやはり気になるポイントですが、今回構築されたAIモデルは実験中のさまざまなトラブルに対応しながら改善を重ねて出来上がったものなので、「AIを入れると現場ではこういうことが起こり得る」という予行練習ができましたし、その積み重ねが「これなら使えそうだ」という安心感につながっていると思います。
野原氏:もちろんメーカーとして品質に関わるような事態があってはならないという思いがある一方で、現場のメンバーが「やってみよう」という前向きな気持ちを持っていたことがプロジェクトを前に進める原動力になっていたように思います。
佐藤氏:内心ではドキドキしていましたが、この取り組みが必ず未来につながるものだと期待していたからこそやり遂げたいという思いがありました。現場の運転員とは常にコミュニケーションをとり、AIモデルが一体どういうものなのか、どれだけ再現性があるものなのか、そしてNTT Comさんへの信頼を伝えていました。
藤井:ありがとうございます。実際にお客さまにお届けする製品をつくっているプラントですから失敗はできないという緊張感がありましたが、私たちに寄せていただいている期待が大きなエネルギーになっています。
野原氏:化学プラントというのは企業秘密の塊なのですが、そこで皆さんが運転員と横並びになって真剣に仕事をされている姿を見て、現場もモチベーションが高まったのではないかと思います。NTT Comの皆さんは非常に熱意を持って取り組んでくださっていますし、「何としても成功させたい」という両社の思いがうまくつながったように感じています。
──製造現場のDXには多くの企業が課題を抱えていますが、本プロジェクトが成功した要因は何だと思いますか。
佐藤氏:知見をうまく引き出していただいたことですね。AIの学習に必要な情報を得るために、あの手この手で質問をしてくださったのですが、同じことでも角度を変えて聞いてくださることで、自分の中にあった知見が発掘されていく感覚があり、それが精度の高いAIモデルの構築につながっていると感じています。また、AIをいきなり現場に導入するのではなく、一つずつステップを踏んでいくので安心感がありましたね。そのプロセスの中で信頼関係を築けたことも非常に大きいと思います。
伊藤:自動運転を実現するには現場の皆さんの知識と協力が不可欠ですから、粘り強くコミュニケーションをとってくださり本当に感謝しています。
佐藤氏:製造現場は刻々と変化していますが、NTT Comさんは変化への適応力がとても高く、それも大きな要因となっているのではないでしょうか。
伊藤:ありがとうございます。オートパイロットのプロダクト開発はNTT Comのメンバーが研究開発、プロダクト開発、事業開発のすべてを一気通貫で行っており、あらゆるレイヤーの課題に対応できる体制を整えています。運転員の操作を学習したAIがプラントの自動運転を行うというソリューションは世界でもまれで、道なき道を切り開くために努力を積み重ねてきたことが、今回の成功に結びついていると考えています。
これまでさまざまな企業を支援してきましたが、今回のようにDX推進部門と製造現場の両者の方々に参加いただけると成功確率が高まるように思います。プロジェクトをリードする野原さん、そして現場を知る佐藤さんがコミットしてくださり非常に心強かったです。
野原氏:気持ちの面で言えば「えいや!」と一歩踏み出せたことが結果として成功につながっていると思います。こういった新しい試みはあれこれと失敗のリスクを考え始めたらきりがありませんから。十分な検討ができているのなら、あとは前を向いて進むのみ。そうした気持ちを強く持てたことが大きいと思います。また機会があればぜひ一緒にチャレンジしたいですね。
──最後に今後の展望をお聞かせください。
藤井:このプロジェクトを通じて、化学プラントの運転がいかに高度な技術を要するのか体感することができました。これからも現場に寄り添い、現場の皆さんの課題解決につながるソリューションを提供していきたいです。
伊藤:私たちの技術やプロダクトは、製造現場を知り、お客さまへの理解を深めていく過程で磨かれていくものです。人間の思考回路をこれほど深く掘り下げてAIモデルに組み込んだ事例は非常に貴重なものであり、今回のプロジェクトで得た学びをより多くの製造現場で生かしていきたいと考えています。
野原氏:私たちもそうなるよう心から願っています。運転員が一人前になるには一般的に数年から10年ほどかかるものですが、人手不足に悩む現場において、人材育成の時間を十分に確保するのは難しいという課題があります。自動運転はその1つの解決策となるものであり、さまざまな製造現場において大いに効果を発揮してほしいと思います。
佐藤氏:今回のプロジェクトを振り返り、製造現場の皆さんがAIなどの新しいテクノロジーを柔軟に受け入れ、積極活用しようという前向きな気持ちを持っていることを感じることができました。「チャレンジしてみたい」と声をあげてよかったなと思いますし、今後も製造現場が進化できるよう挑戦を続けていきます。
OPEN HUB
Theme
Co-Create the Future
#共創