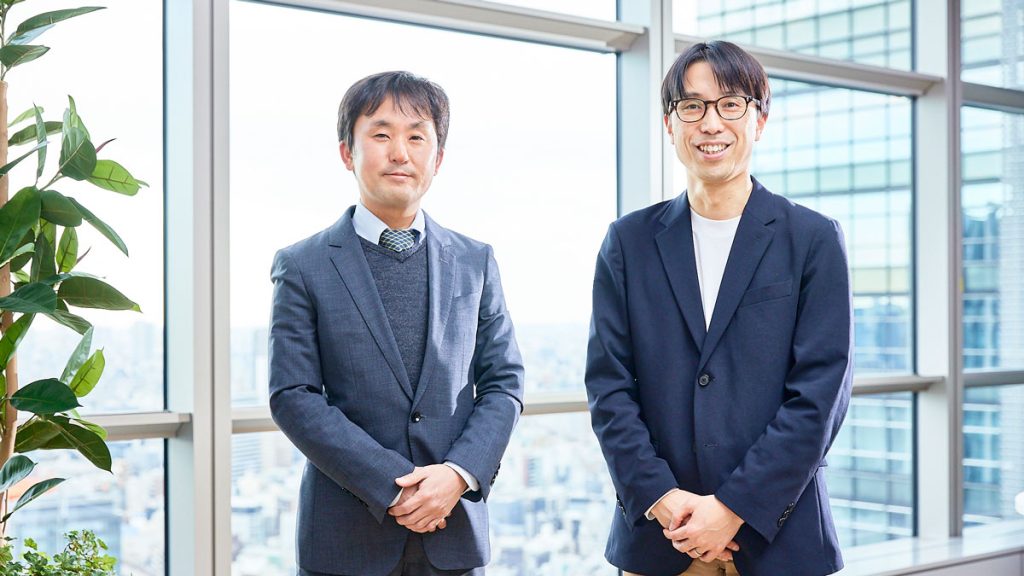
01
2025.03.06(Thu)
Future Talk
2022.03.30(Wed)
目次
——日本では、IoTやデジタルツインを使ったものづくりやAIの工場での活用といった製造業のDX化が進んでいるとは言い難いと聞きます。何が障壁になっているのでしょう?
西岡氏:DXに限らず、そもそも日本のものづくりの現場はIT活用力が低い傾向があります。理由は日本の強みでもある“現場力”が高すぎるから。工場などの製造業の現場には素晴らしい職人のようなオペレーション技術が根づいており、材料のバラつきや甘い設計があっても現場で臨機応変に対応できます。「なんとかする」だけではなく、現場の力で極めて質の高いものをつくりあげてきた歴史があるのです。
一方、IT活用は、パッケージソフトのような標準的な仕組みを現場に取り入れること。効率化を図り、ニーズに沿った多品種少量生産などにも対応できますが、日本の強みである現場の力、臨機応変さや独創性が削られる可能性もあります。結果として、今なお「ITの積極活用は、競争力が下がるのではないか」との危惧が色濃く残っているのではないでしょうか。
——DXにおいても同じ意識が働いているわけですね。
西岡氏:はい。しかしグローバルなものづくりの世界ではDXはすでにスタンダードです。工場内の工作機械にセンサーを取り付けて稼働状況などをデータにして見える化、プロセス改善を果たしている工場は数多い。DXを図れなければグローバルなバリューチェーンの中に入れなくなります。
——一方の伊藤さんはNTTコミュニケーションズで先進的なスマートファクトリーの取り組みをリードしています。最前線で感じる製造業DXの課題、障壁はどこにあると考えていますか?
伊藤:私はまた別の角度から製造現場の強さがハードルになる状況を実感した経験があります。AIを活用した化学プラント業界のDXを図ろうと、工業計器やプロセス制御システムの販売、保守サービスを提供する横河ソリューションサービスとパートナーシップを組んでいますが、当初は従来の運転員が考えもしない最適な制御方法をAIが自律的に獲得する仕組みをつくろうとしていました。イメージしたのは「アルファ碁」。AIが仮想空間上で試行錯誤を重ねることにより、人間のトップ棋士をも超えた囲碁プログラムです。それを工場でも実現できるのではないかと考えていました。
伊藤:まずは温度、圧力、流量など、プラントのさまざまなデータをセンシングして集め、学習した機械学習モデルと、現場で使われている制御アルゴリズムを組み合わせることによって、デジタルデータ上のプラント(プラントデジタルツイン)を開発し、将来の状態を予測します。このデジタルツインに対して、AIが強化学習による試行錯誤を行うことにより、人間がこれまで動かしてきたプラントのオペレーションを超えるような高い制度の制御や、効率性を図れるのではないか。その先にプラントの自動制御もかなうのではないか、と考えたのです。
——アルファ碁のように人間を超えたプラント制御AIですね。世界でもまれなチャレンジだったのではないでしょうか。
伊藤:はい。しかし、結論から言うと不可能でした。化学プラントは極めて複雑な物理法則に基づいて化学反応が起こっており、なぜ触媒を入れると反応が活性化するかですら、明確に分かっていないんです。突き詰めると量子力学のような世界に基づいてプラントが動いていると思われ、いくらデータを集めてもシミュレーションできない部分がある。しかも、一見同じように見えるデータも、天候や運転条件によってどんどん変わってしまう。蒸留塔のように、比較的単純な工程では実現できたのですが、リアクター(反応炉)まわりは特に複雑で、プラントデジタルツインを開発できませんでした。要するに、常に状態が変化し、AIでモデル化することができないような複雑な工程のオペレーションを、現場のオペレーターの職人的な手作業が支えていた。彼らを超えるオペレーションをDXで成し遂げるには、ハードルが高すぎました。
——DXを凌駕する現場力を、目の当たりにしたのですね。
伊藤:印象的だったのは、現場のオペレーターの方が「以前、広島の製造業にいたんだけど、その頃のオペレーションの知見をうまく使うと、そこそこ運転できるんだよね」とおっしゃっていたこと。人間は複雑なデータを正確に処理するのではなく、本来複雑な操作を大づかみし、一般化して転用するという高度なオペレーションをしているんだとあらためて実感しました。そこで、アプローチを変えることにしたんです。プラントそのものをデジタルツインにするのではなく、プラントを制御している「オペレーターのデジタルツイン」をつくる方針に変更しました。
——プラントではなく人間をデジタルツイン化するのですね。
伊藤:熟練したオペレーターが、時々刻々と変化する環境の中で、プラントの制御をどのように行っているか、それを学習してデジタルツインにします。そのうえでプラントからセンシングした運転データをオペレーターのデジタルツインに走らせる。これにより、熟練オペレーターのような優れたオペレーションをAIで再現できるようになります。それまでオペレーターが変わると原材料の量や投入のタイミングに差が出ていましたが、運転の均一化が図れるだけでなく、AIがどのように結果を導いたのかも併せて提示されるので、困難だった技能伝承が支援できるんです。NTTコミュニケーションズが開発した「Node-AI」というノンコーディングでAIモデルが作成できるツールを使用し、オペレーターが持つ現場の知見、横河ソリューションサービスが持つプラント制御の知見、NTTコミュニケーションズが持つ製造業向けデータ解析の知見を組み合わせてAIモデルを開発しています。
西岡氏:ギリギリを攻めた最先端のお話、興味深いです。デジタルツインがなかなかうまくいかない部分にもとても共感します。私は、当初から製造業のデジタルツインは諦めていたので……。
——デジタルツインを諦めた、とはどういうことでしょう?
西岡氏:正確に言うと、サイバー空間上にリアルと同じものをつくるとデジタルツインはいろいろな効果があると思っています。諦めたのは、シミュレーションによって、未来予測する部分です。デジタルツインによってリアルのものづくりの精度を上げ、効率化を図るというコンセプトはもちろん正しい。けれど、伊藤さんの化学プラントの例でも分かるように、あまりに複雑な現場ではリアルの置き換えすら難しい。生産現場は例外の塊ですから。
デジタルツインを完成させるために、個別のパースを組み立てていくと、人間が担当する部分が埋まりません。AIが完全に仕事にとって変わることができないのと同じ理由です。ならば、人間でしかできない部分を残してつなぎ合わせる必要がある。先に述べた、日本のものづくりの強さ=現場力を残したDXの方向性がそれだと考えています。
伊藤:私はまだプラント自体のデジタルツインを諦めてはいませんが、確かにゴールはまだまだ先だと認識していますね。人間は1つ教えたら一般性を見いだして3つ知るような高度な学習ができるし、さまざまなデータを環境の違いを取り除いて一般化できる。しかし、AIは1万のデータを教えて、やっと1つ知るような面があり、人に比べて知識の一般化が圧倒的に苦手です。人間が持つ「学ぶ力」のようなものを現場のドメイン知識と共に、うまくAIと組み合わせられないかなとも考えています。
——そうした現状を踏まえ、日本の製造業はどのような姿勢でDXに臨めばいいのでしょうか。
西岡氏:経営層は「製造現場がバリューを生む」とあらためて捉え直すべきだと思います。製造業のバリューチェーンでは、企画やマーケティングなどの上流と、川下にあたるアフターサービスなどの下流、その両端が「付加価値が高い」とされています。上流と下流をつなぐ製造部門は付加価値の対象ではないと思われている場合が多い。そのため、製造部門はとにかくコスト削減だけを命題とされ、投資しようとしてきませんでした。
しかし経済のデジタル化がますます進み、サプライチェーンの中でユーザーのニーズや製造環境の変化に対応するには、そうした変化を瞬時にくみ取って適切な生産をしていく生産現場が不可欠になっています。強靭で効率的な製造現場が、潜在的な価値を現実のお金に換える鍵であると経営層が認識して、DXに取り組む製造現場へ積極的に投資をする必要があります。その実現なくしてグローバルな競争に太刀打ちできません。
——伊藤さんはどう思われますか?
伊藤:私が見た限りでは、自社内の価値あるデータが埋もれたままの状況が多いと感じています。先ほどの「広島の製造業でのノウハウが別の工場の化学プラントのオペレーションに活きた」とおっしゃっていたオペレーターの方の知見、あれはその方が異動してきたのでノウハウとして発掘されました。こうした現場の暗黙知のようなノウハウは、転用可能な価値あるデータとして活きる可能性が高いと感じます。しかし、同じ工場内、会社内でも共有されていない。ましてや企業を超えた連携はほとんどできていないので、うまくこれを共有する仕組みづくりが必要だと感じます。
——まさにIVIが標榜しているプラットフォーム、「日本の現場の強みを生かしたDXの形」の役割ですね。
西岡氏: IVIはキーコンセプトに「つながるものづくり」と「ゆるやかな標準」を掲げています。日本ならではの現場の独自性を残しつつも、標準化できる部分は標準ルールと仕組みに基づいてデータを共有し、業種や領域を超えて会社や工場をつなげます。現場の知見を2割ほど残しながら、ゆるやかに標準化した共通言語とシステムによって残りの8割ほどをゆるやかにつなげるのです。これを実現させるため、250社超の会員が、毎年20前後のテーマのワーキンググループで活動し、日々前進させています。
——「ゆるやかな標準」によって現場の強みを維持しながらも、ダイナミックなグローバルのバリューチェーンともつながれるわけですね。
西岡氏:製造現場は昔から標準化には前向きです。しかし外部から「グローバル標準に合わせなさい」「他社と共通化しなさい」と言われると反発しがちです。「先輩から伝承した今のやり方でまわっているのだからいいじゃないか」となってしまう。
伊藤:それこそが独自性で強みでもあるのなら、そこはいじらず、共通化する仕組みはつくっていきましょうと。
西岡氏:先ほどの「広島の製造業での知見」のような例が自社内でも見える化されるし、他の会社や産業で生かされる可能性も高まります。こうした知見をデータとして共有できれば、その会社の製造技術は製品のライフサイクルの終了後であっても、別の製品の中で新たな技術として進化する可能性が飛躍的に高まります。また、現場から得られるデータは、機密性を担保した形で、企業間で個別に共有するサービスも提供されはじめています。
伊藤:製造業の現場を出入りしていると「かつてより現場力が落ちてきている」との声が聞こえます。今のうちに現場の知見を残していくのは我々の使命だと感じていますし、IVIのプラットフォームづくりへの期待も高いです。今後もデジタルと人の融合を一層すすめていきたいですね。
西岡氏:「ゆるやかな標準」と「つながるものづくり」によって、2030年くらいには日本の工場は3つの形に変わると考えています。1つは消費者に近い場所に設計図データを転送して3Dプリンティングによる部品製造や組み立てなどの最終工程を手掛けられる「コンビニ工場」。2つめが専門性が高く大規模な投資が必要な特定の製造工程に特化して請け負う「シェアリング工場」。そして最後がコアコンピタンスに関する製造知識やノウハウといった知財を強みとして系列などを超えて自在に他の製造業とつながる「コネクテッド工場」です。
いずれもデジタルデータでつながっているからこそ実現できる未来であり、すべてに企業を越えて新たな価値を生み出す“共創”の思想が基盤にある。現場の強さは残しつつも、事業部や企業の垣根を越えて「多くの仲間とつながるためのマインドセット」を獲得することが、とても大切だと考えています。
NTTコミュニケーションズ スマートファクトリー推進室の取り組みはこちらから。
OPEN HUB
THEME
Future Talk
#専門家インタビュー